
In today's era of rapid industrial development, aluminum die casting technology has become one of the important forces to promote the progress of the manufacturing industry. With its high efficiency, high strength and low cost, this technology has been widely used in the world, especially in the production of motorcycles and auto parts.
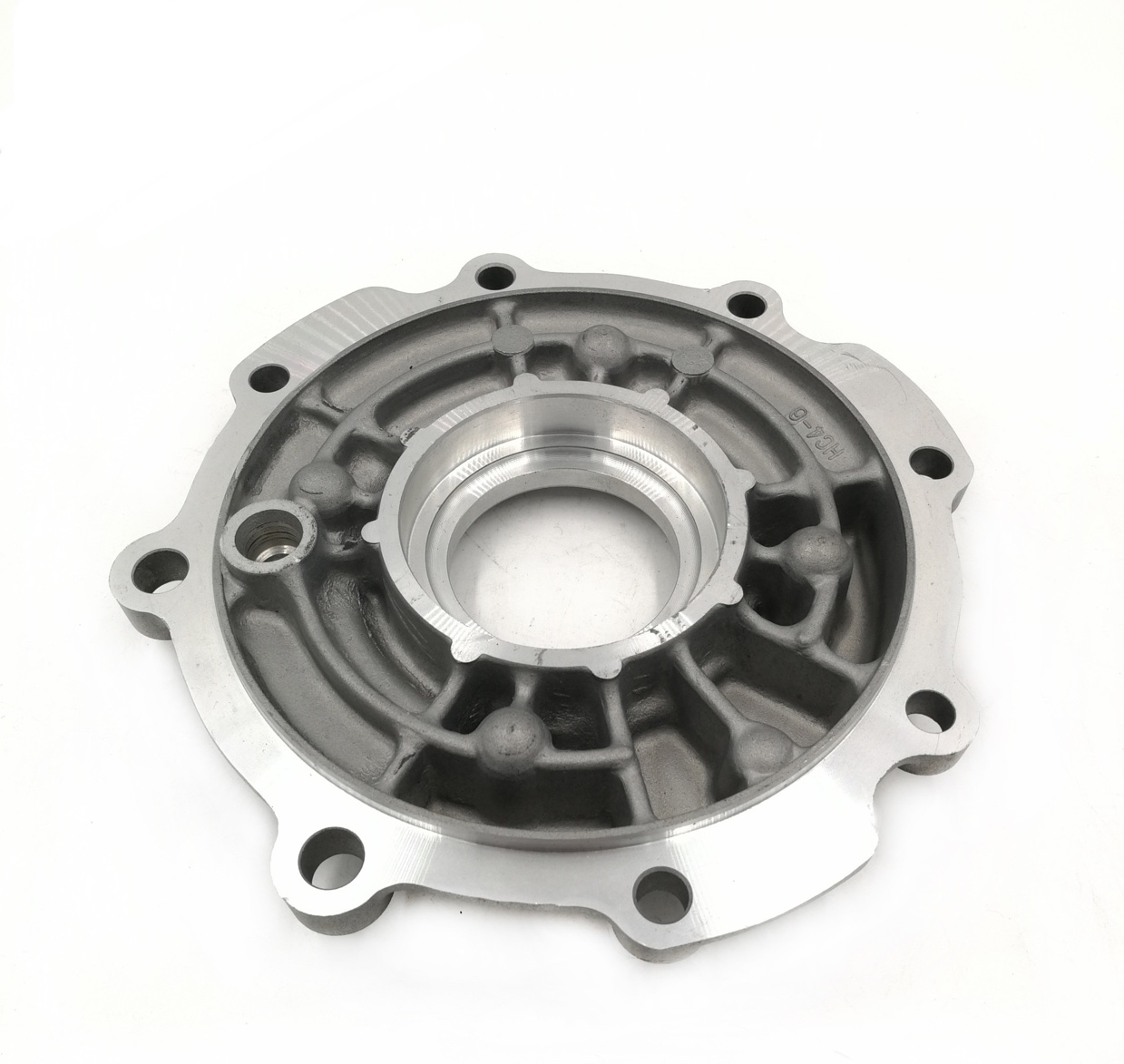
So what exactly is aluminum die casting? Simply put, this is a process of injecting liquid aluminum alloy into a mold cavity under high pressure to form a specific shape. Compared with traditional casting methods, this method can significantly reduce material waste and increase the complexity of the product, so as to meet more customized needs.
Why more and more companies prefer to choose aluminum alloy as the main raw material? This is due to its excellent physical and chemical properties-not only has good thermal conductivity and corrosion resistance, but also has an excellent strength to weight ratio, making it an ideal choice for vehicle weight reduction and energy saving. In addition, with the increasing awareness of environmental protection, the characteristics of high recycling rate also make aluminum alloy favored.
Every step of the process is critical, from the beginning of the research and development phase to the completion of mass production. For example, in the design process, it is necessary to fully consider the rationality of the runner arrangement and the effectiveness of the exhaust system, while in the actual operation process, the temperature parameters must be strictly controlled to ensure the uniform and stable fluidity of the molten metal. These seemingly cumbersome but indispensable small details together determine the quality of the final product.
It is this attitude of excellence that has resulted in many amazing works. For example, the brake disc components used for precision braking systems on high-end motorcycles or the complex suspension arm structures under the hood of luxury cars, etc., all reflect the highest level of achievement in the field of contemporary engineering. Behind every tiny component, there are countless figures of scientific researchers who have worked hard.
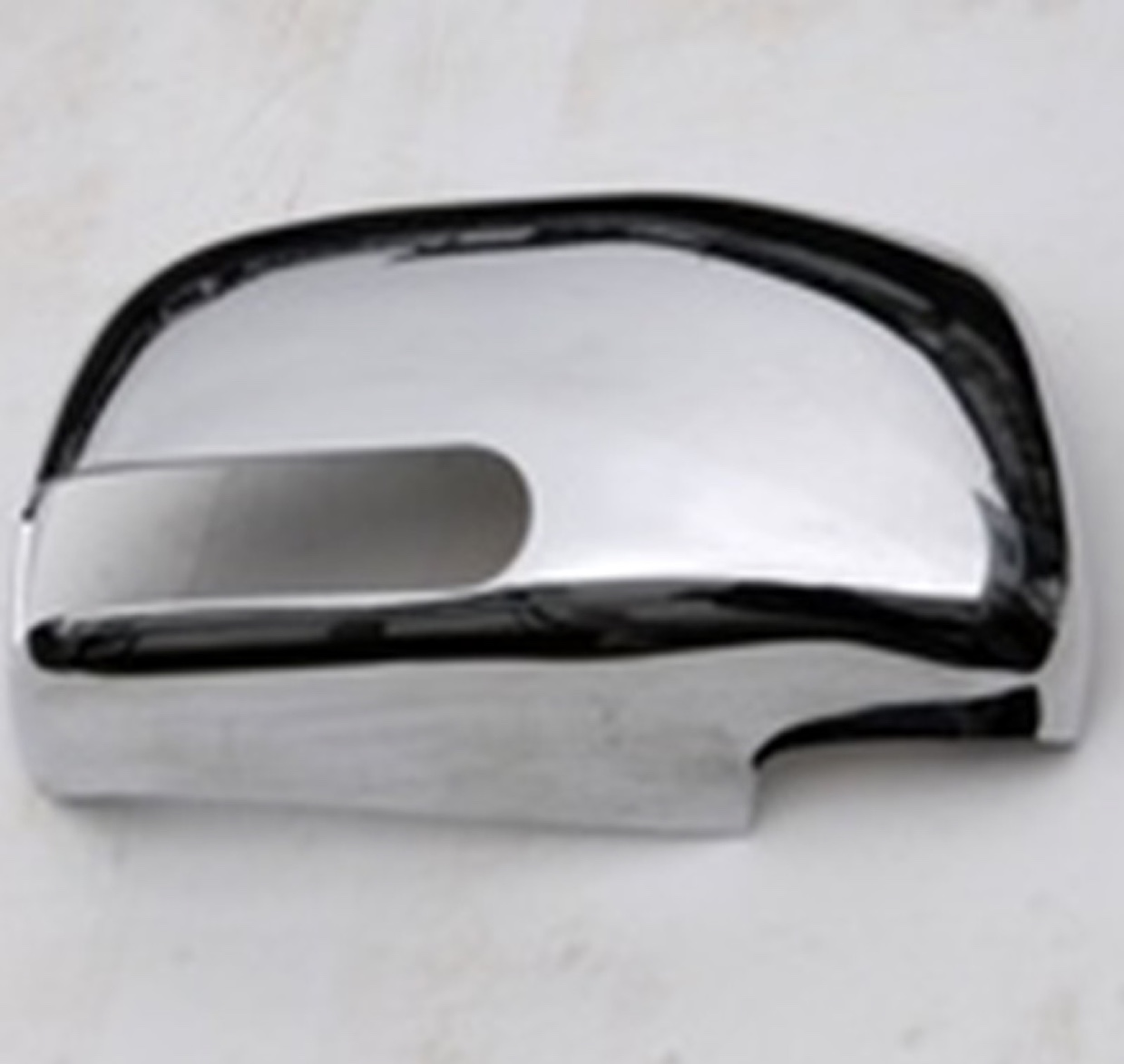
Nowadays, both professional racing drivers who pursue fast passion and ordinary consumers who commute everyday can enjoy the safe and comfortable experience brought by advanced technology. A large part of the credit is due to the unknown contribution of the high quality parts produced by the latest generation of aluminum die-casting technology.
Looking to the future, intelligent automation will become a major trend in the development of the industry. With the help of big data analysis to predict potential failure risks, it is possible to take preventive measures in advance. Additive manufacturing (I. e. 3D printing) is expected to further shorten the development cycle of new products and reduce the proportion of cost expenditure. All this will promote the whole industry chain to a higher level.
All in all, with excellent performance and broad market prospects, it is no exaggeration to say that high-quality aluminum die-casting technology has become an irreplaceable core competitiveness in the field of motorcycles and automobiles in the new era.
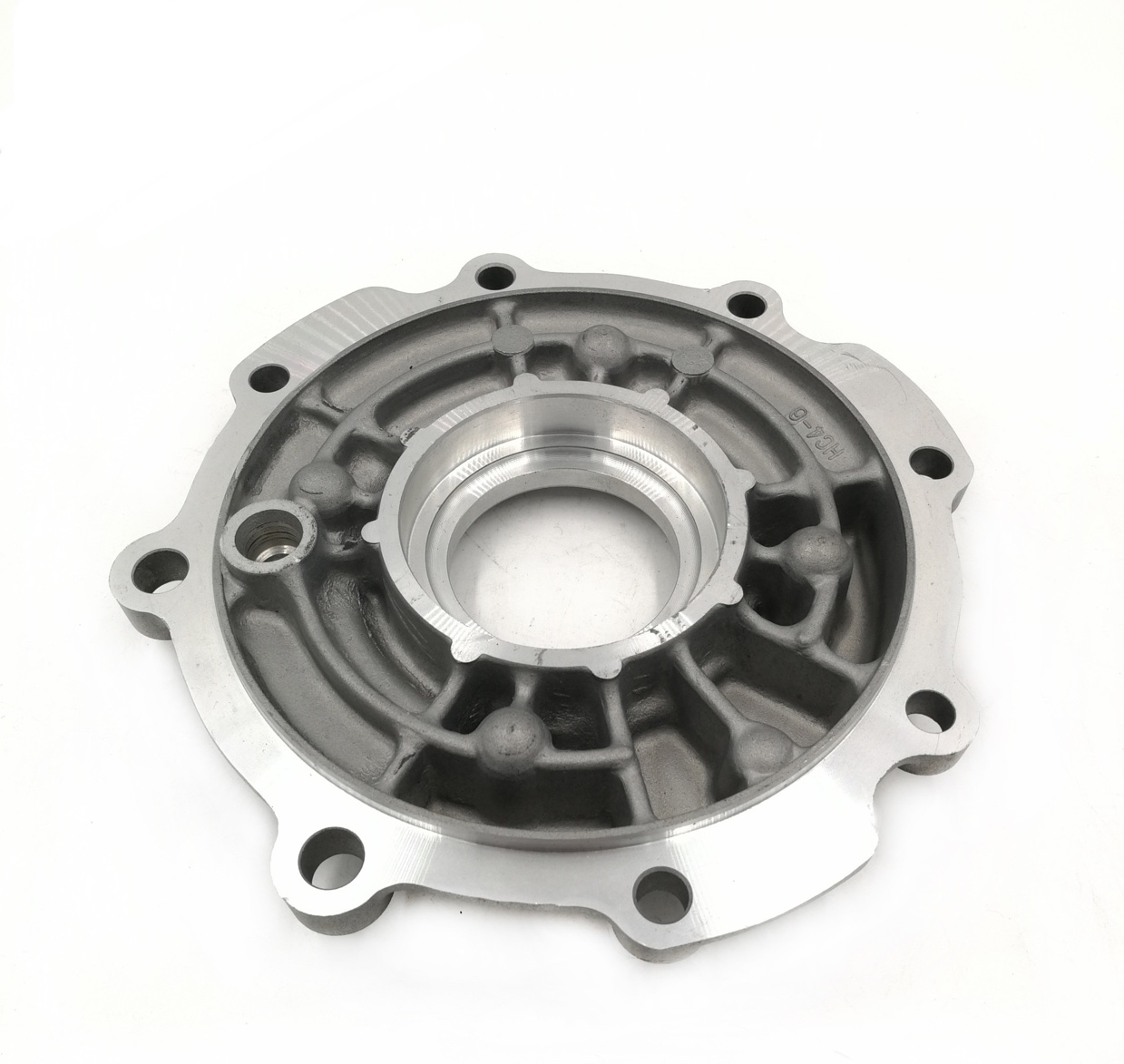