
In modern industry, aluminum alloy has become an indispensable part of many fields due to its excellent properties. Especially in the motorcycle and automotive industries, parts produced through advanced aluminum die-casting processes not only improve the overall performance of the vehicle, but also extend its service life.
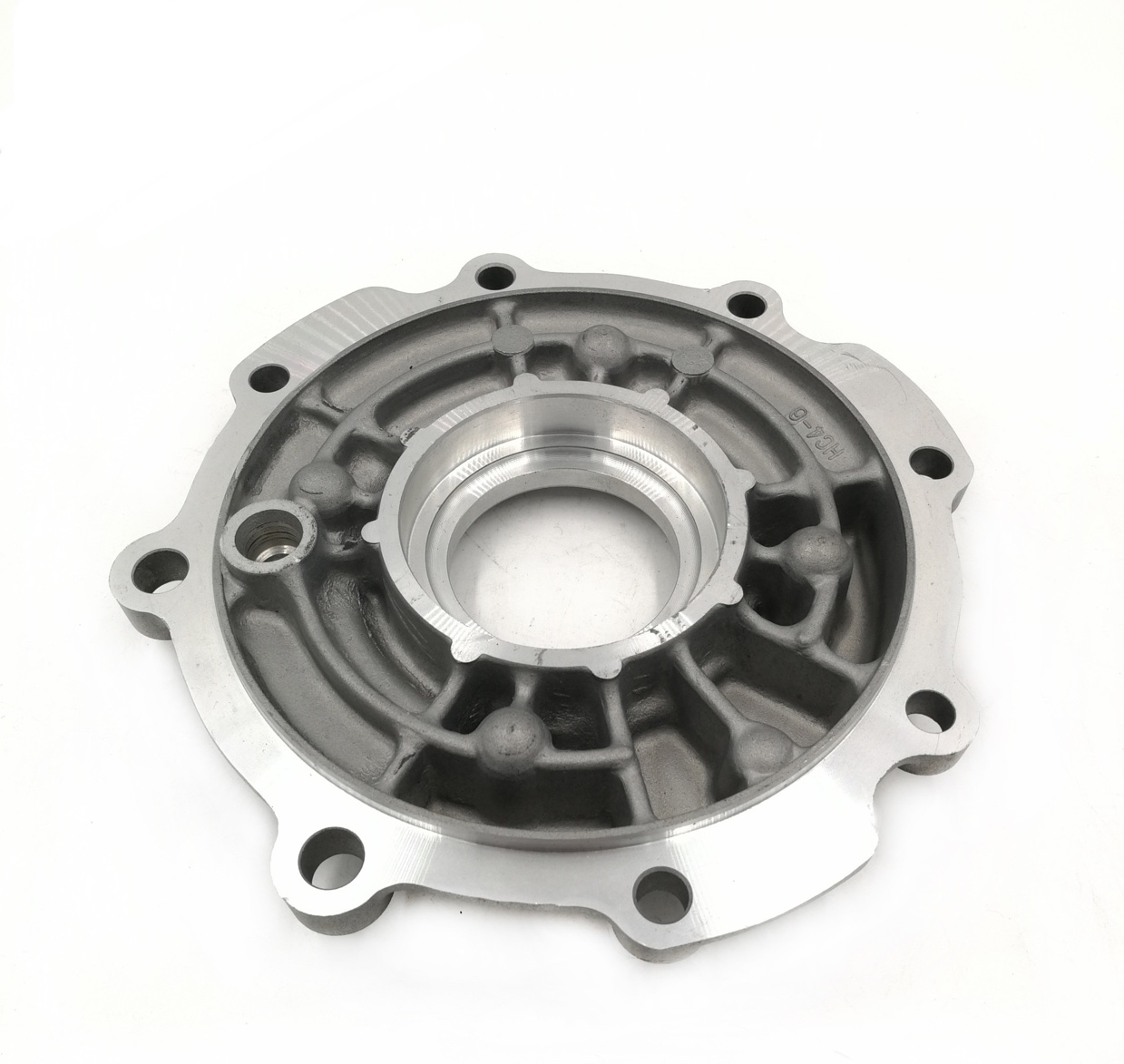
From raw materials to finished products: the secret of the high quality aluminum die casting process
high quality aluminum die-casting is not an overnight process, but the result of careful design and technical polishing. First of all, the selection of high purity aluminum alloy as the main raw material, this step determines the basic quality of the whole product. Subsequently, the alloy is melted into a liquid state under high temperature conditions and injected into a precision mold for rapid cooling molding. Finally, detailed processing, including surface polishing, heat treatment and a series of processes to achieve the standard specifications required by customers.
The core of industrial manufacturing: why aluminum alloy is the ideal material for motorcycles and auto parts
Compared with other metal materials, aluminum alloy has the advantage of light weight and high strength, which is very suitable for vehicles that need to balance speed and durability. For example, the common wheels, engine cylinder heads, and chassis brackets on motorcycles are all made of this material; and the brake discs that are vital in the car brake system are also inseparable from it-because it can withstand The heat generated by frequent and severe friction is not deformed and damaged.
Behind the Stable Quality: How Professional Manufacturers Ensure the Reliability of Every Product
An excellent enterprise must have a perfect quality management system throughout. From the initial research and development stage to the final delivery to the customer, the inspection standards must be strictly implemented to ensure that there are no defects. For example, the use of X-ray flaw detector to check whether there is a hole defect problem or the use of three-coordinate measuring machine to accurately verify whether the size meets the requirements of the drawings and so on are widely used.
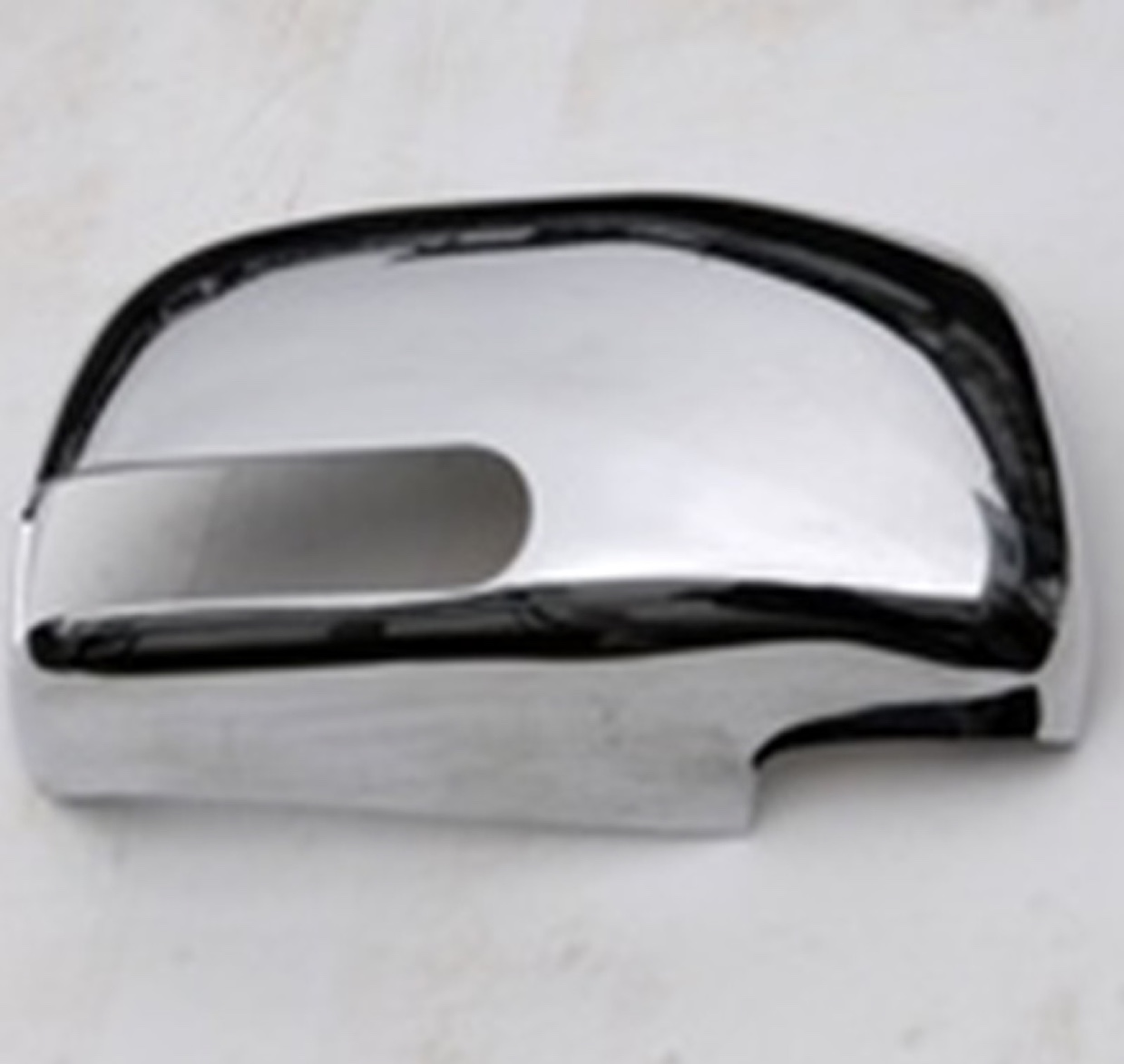
Application scenario analysis: the important role of aluminum die castings in brake pads and other key components
Take brake pads as an example, this is one of the most sensitive links related to driving safety. Because it is in high-speed operation for a long time and will encounter various harsh environmental factors (such as rain erosion), it is necessary to choose materials with strong corrosion resistance and good heat dissipation efficiency. The special grade aluminum alloy prepared by the specific formula can meet all the above conditions and is widely used in actual production.
Future Trend Outlook: Impact of New Energy Vehicles and Intelligent Equipment on Aluminum Die Casting Industry
With the global promotion of the concept of energy saving and emission reduction deeply rooted in the hearts of the people and the trend of technological progress to promote the increasing number of electric vehicles, the traditional fuel power device is gradually eliminated and replaced by the battery pack drive form. This means that more new components will be born that require high-performance lightweight solutions to achieve the desired goals. So it can be said that now is the perfect time to plunge into this dynamic field!
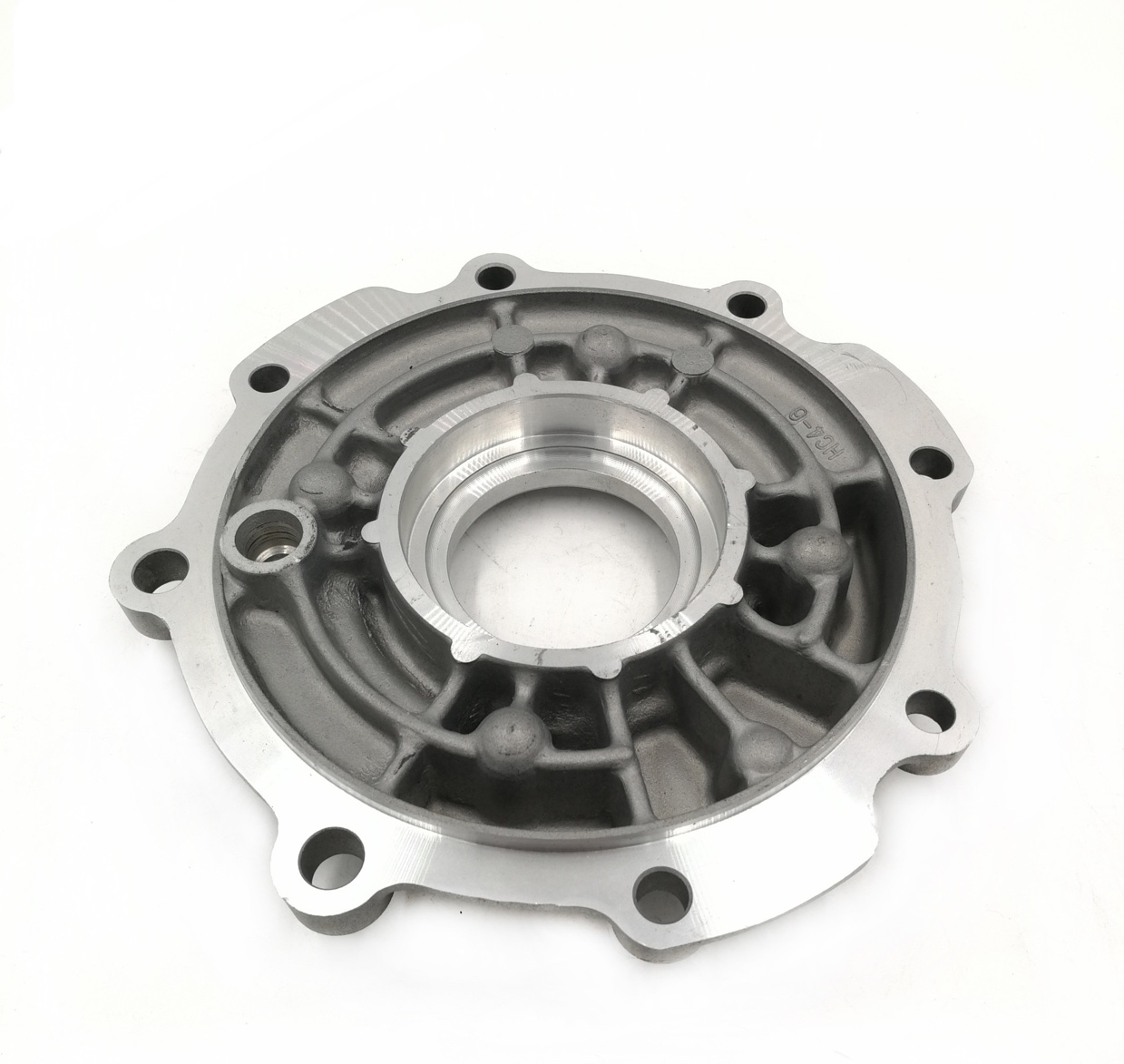