
In today's era of rapid technological development, lightweight, high-strength materials have become an indispensable part of the manufacturing industry. Among them, aluminum alloy stands out for its unique physical properties and excellent mechanical properties, and has become a star material in the modern industrial field. Especially in the field of vehicle manufacturing, whether it is high-end racing or daily scooters, aluminum alloy die-casting parts play a vital role.
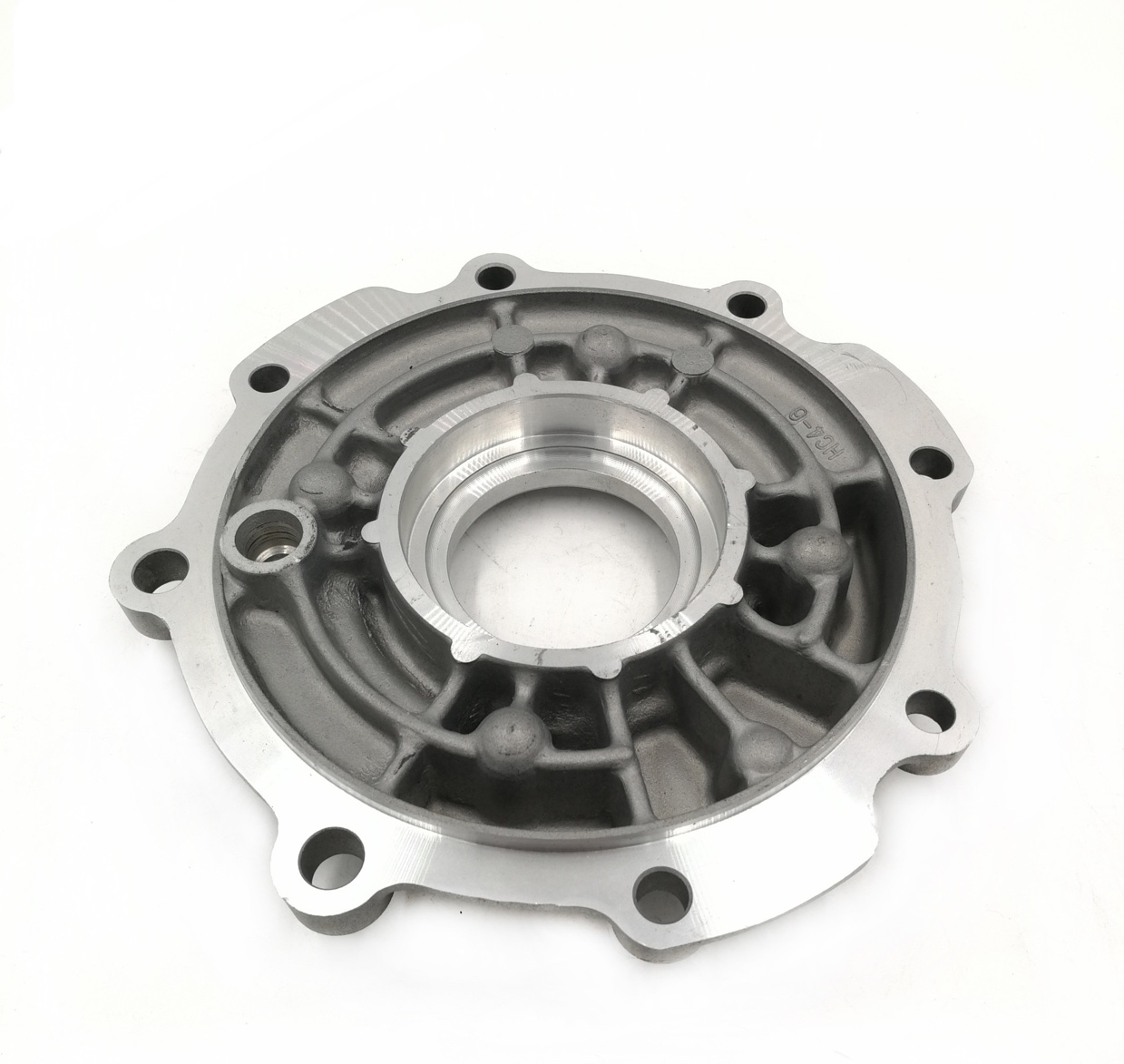
Our production process begins with a careful selection of quality raw materials. The birth of each product has gone through numerous tests and adjustments to ensure that the selected aluminum alloy composition reaches the optimal ratio, so as to maximize its strength, toughness and corrosion resistance. Then it enters the casting stage, and the molten metal liquid is injected into the mold cavity under high temperature environment and then rapidly cooled and formed. This link requires extremely high precision control and rich experience to achieve the desired results.
These finely crafted aluminum alloy components are widely used in the motorcycle and automotive industries. For professional riders who pursue the experience of speed and passion, an engine housing equipped with an efficient heat dissipation system is essential. For family users who pay attention to comfortable driving experience, they can choose to install gearbox components in a more quiet and stable operation mode to enhance the overall driving pleasure. At the same time, in terms of braking systems, high-performance brake discs made by special treatment processes can maintain stable working conditions under extreme conditions, which greatly improves driving safety.
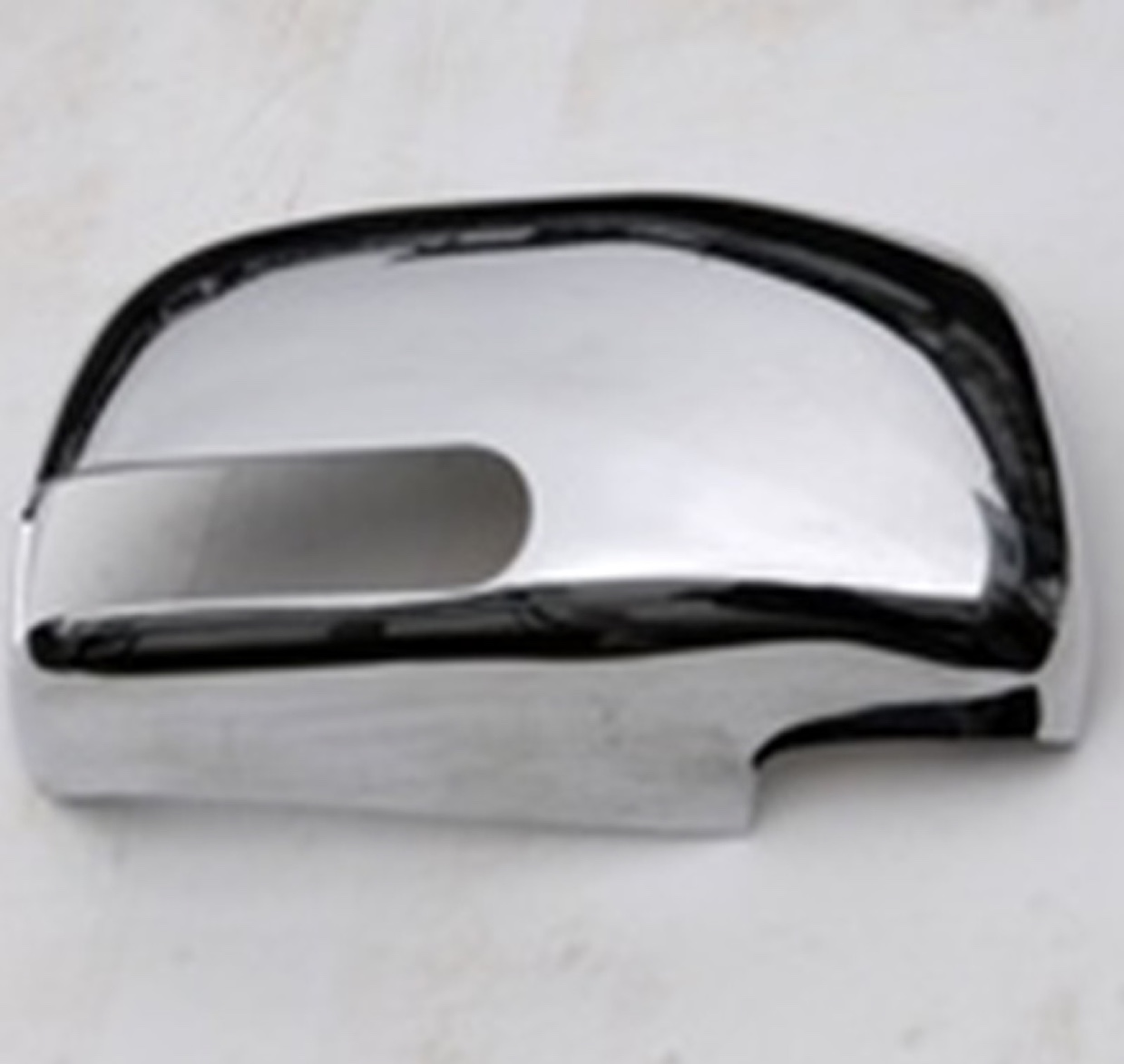
In order to provide customers with reliable and durable products, we have established a complete quality management system throughout the entire R & D production and after-sales service process. From the initial design drawing review to the final finished product packaging before leaving the factory, it must go through multiple inspection steps, including size measurement, surface finish evaluation and internal organizational structure analysis, etc. Only when it fully meets or even exceeds the expected standards can it be officially put into the market.
Looking to the future, with the deepening of new materials research and technological innovation, aluminum die casting industry will usher in more development opportunities. Intelligent robot-assisted operation can not only greatly reduce labor costs, but also significantly improve work efficiency, while the application of additive manufacturing technology opens up a new space of possibilities for complex geometric components. It is believed that more and more amazing works will come out soon to continue to push forward the pace of human civilization.
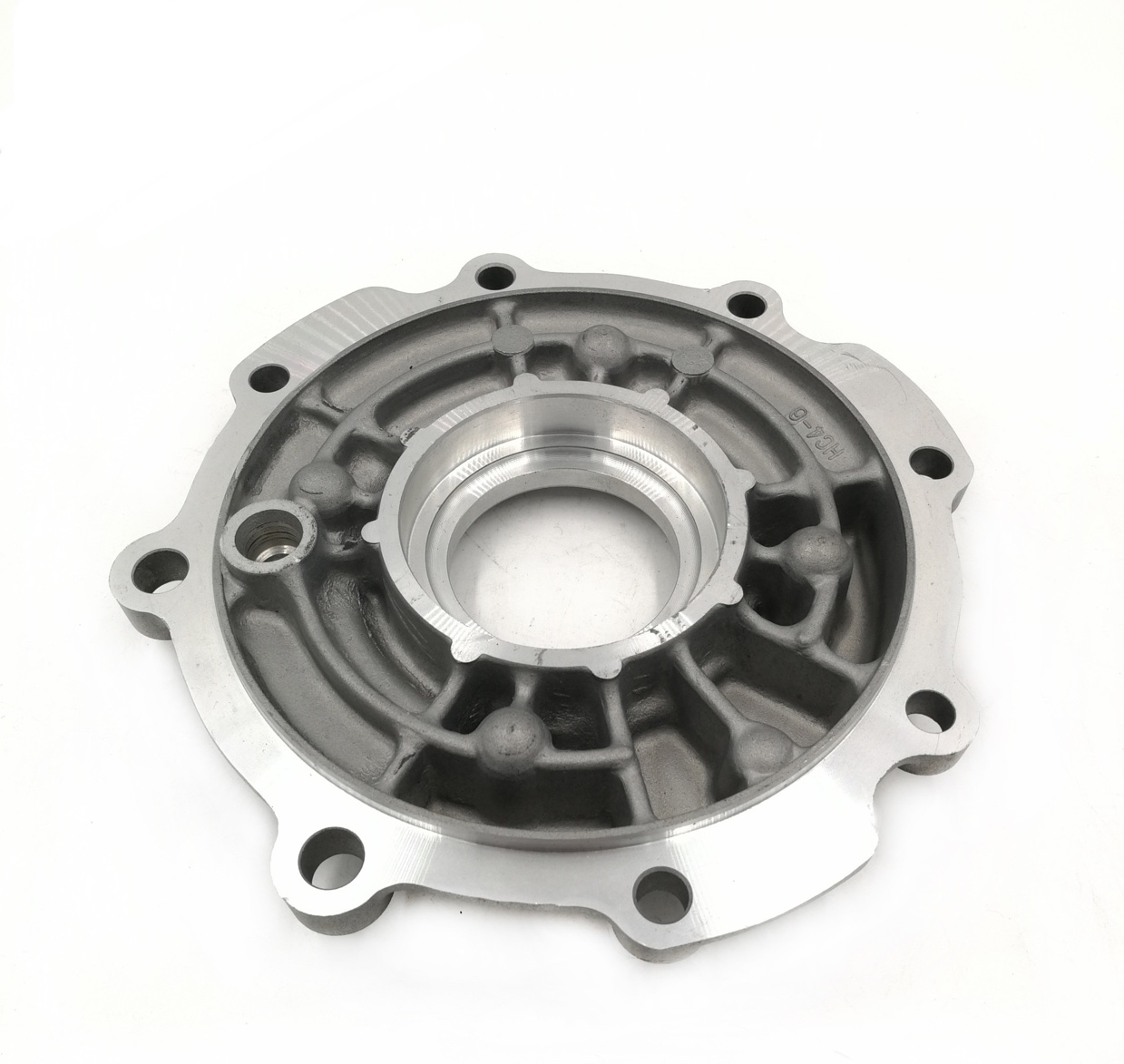