
Uncovering the mystery of aluminum die casting: the core power of technology
Let's go into the world of aluminum die casting and explore this ancient and advanced metal forming process. Aluminum die-casting is a process in which molten (liquid) aluminum alloy is quickly filled into the mold cavity under high pressure, and the finished product is removed after cooling and solidification. The whole process includes carefully preparing the mold, heating and melting the aluminum into a liquid state, and then injecting it into the preset model to complete the curing.
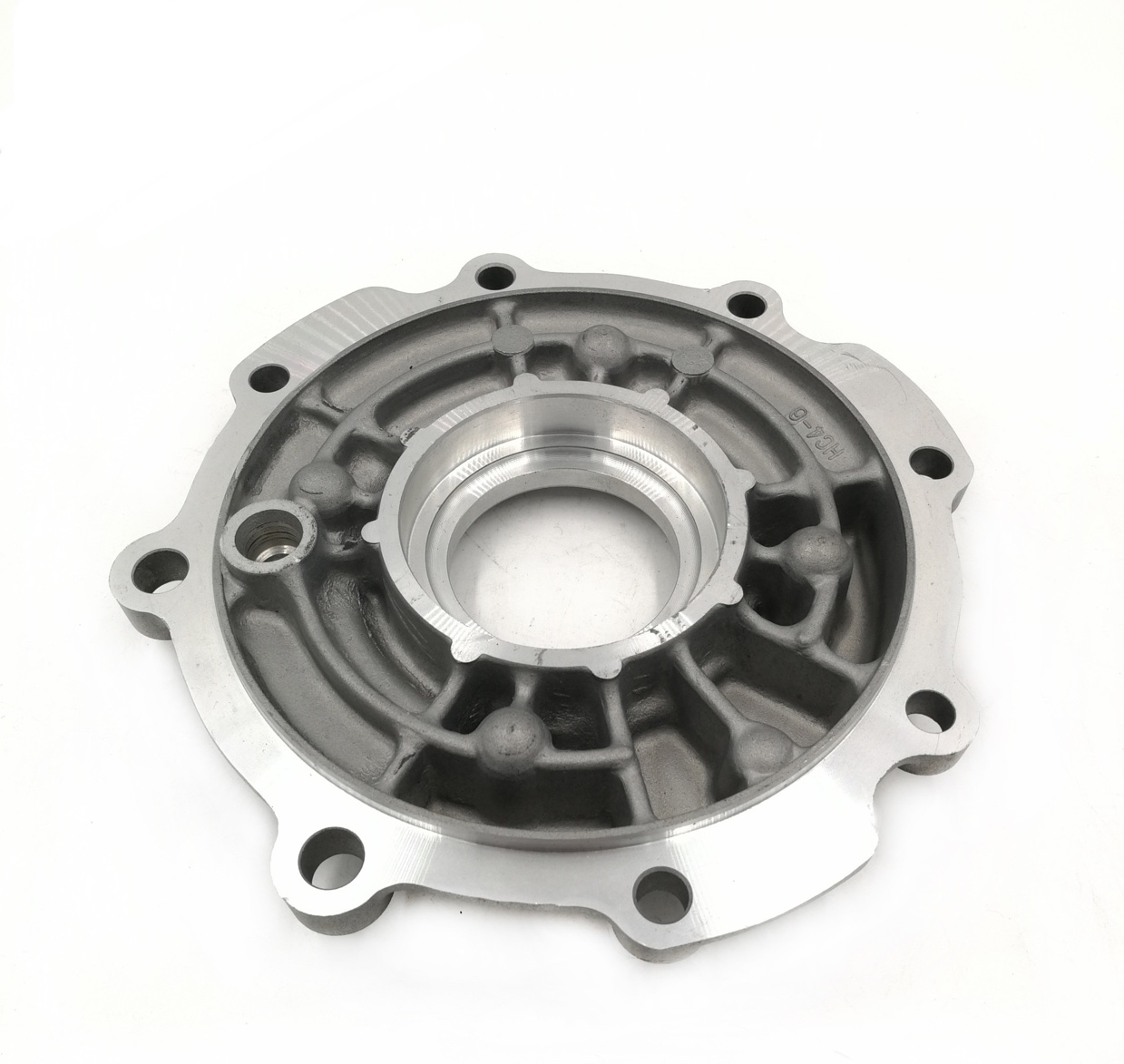
The biggest advantage of this technology is that it can produce parts with complex geometries and very high precision, which is difficult for other casting methods to match. Compared with the traditional forging method or other forms of pressure casting, aluminum die casting not only improves the production efficiency but also greatly reduces the cost input, especially suitable for large-scale industrial production.
From the factory to the street: the charm of direct supply of high quality parts
Nowadays, more and more manufacturers choose to adopt a direct sales model to sell their motorcycles and auto parts. The biggest highlight of this approach is the need for unnecessary intermediate links, which brings multiple benefits. The first is the impact on the price. After removing the price increase, the product price is often more competitive. Secondly, the delivery speed is obviously faster, because it can directly meet the customer's needs and arrange the delivery. Finally, the quality supervision is more strict and reliable. As the number of turnover is reduced, it is easier to trace the source to ensure that each batch meets the high standard requirements.
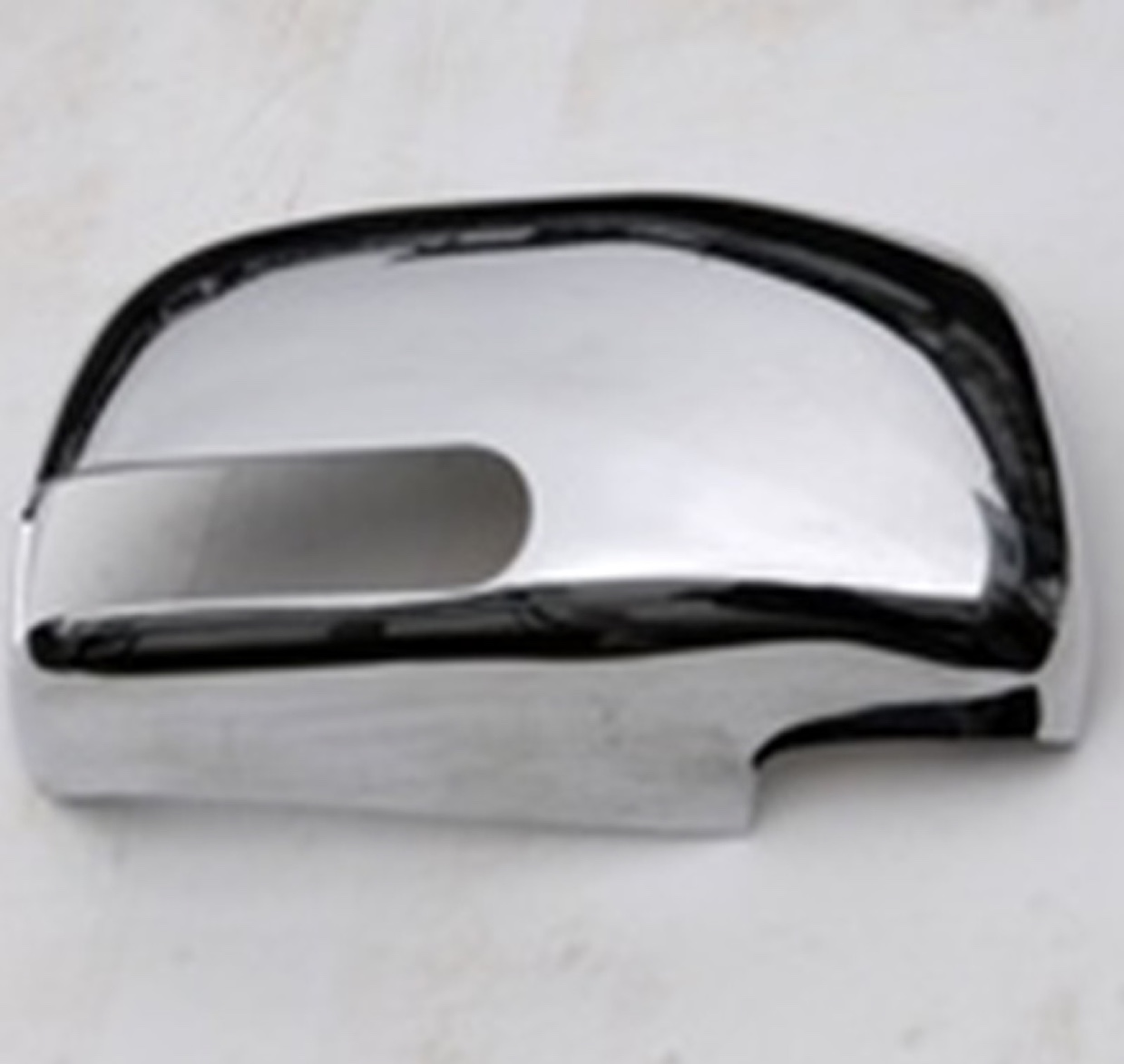
For the majority of motorcycle enthusiasts, such a supply chain is undoubtedly a great boon. It not only provides a richer purchase options, but also enhances the stability of product supply, so that car owners can rest assured to choose the most suitable accessories without worrying about the supply of goods. Whether it is daily maintenance or modification and upgrading, there are more diversified choices.
Safety guardian of key parts: brake pads and other core components
When it comes to vehicle safety, the most important part of the system is the brakes. And one of the decisive role is the small but extremely critical brake pads. Brake pads produced by the aluminum die-casting process have a higher level of heat resistance and wear resistance. These two characteristics allow it to function without compromise when braking frequently under high-speed driving conditions. In contrast, traditional materials may suffer performance degradation or even failure due to excessive temperature or excessive friction.
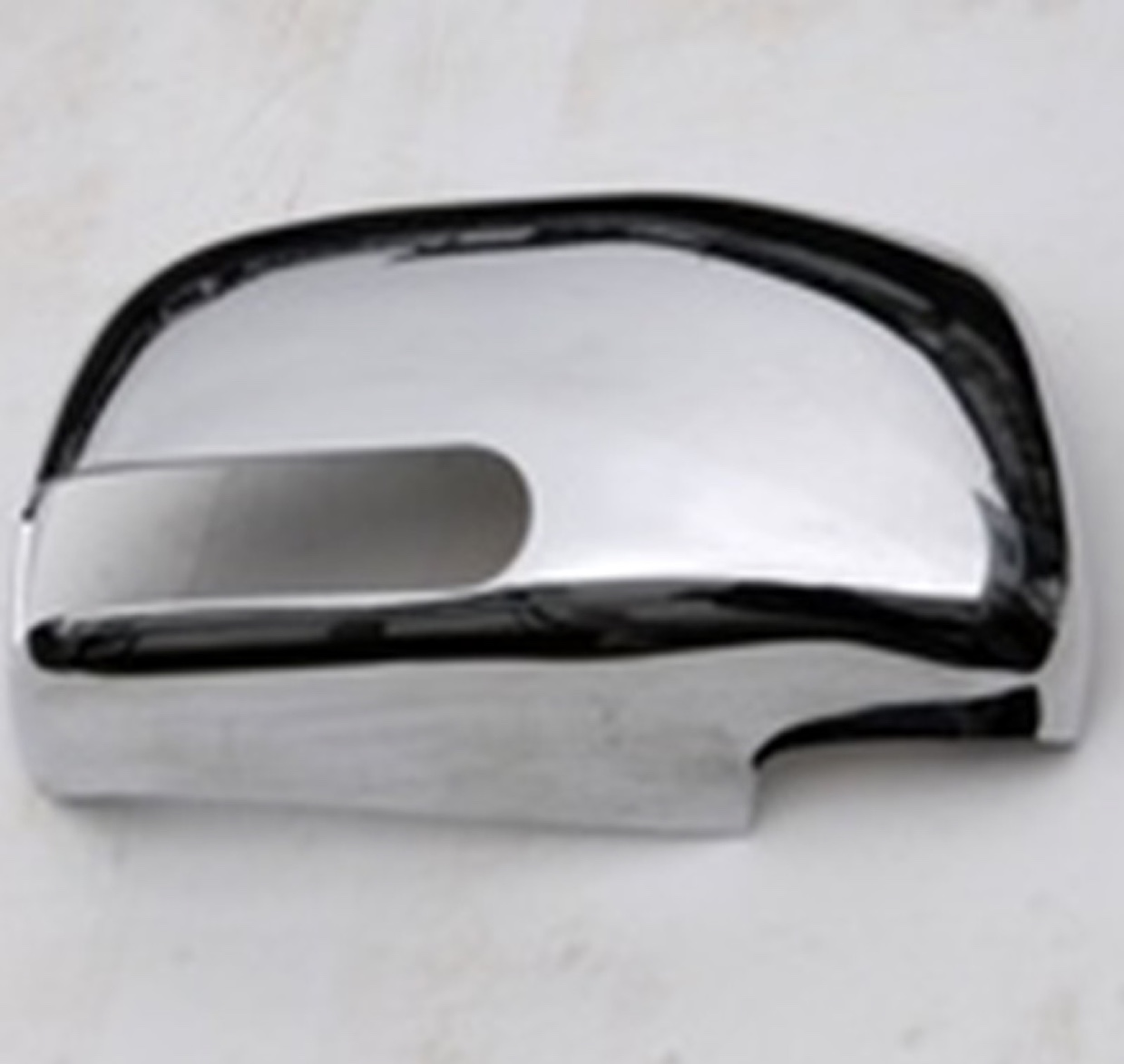
In addition, there are many small parts made of aluminum die-casting also play an important role in vehicle performance, such as wheels and hood panels. Although they may seem trivial, they directly affect the driving experience and overall safety. It is these high-quality components that make up the rugged and sensitive modern vehicles we see on the road today.
The Art of Precision Machining: The Secret to Flawless Products
Every subtlety embodies the hard work and technical crystallization of the craftsman. The modern production workshop is equipped with the most advanced production equipment and rigorous quality inspection procedures, and strive to make every factory product reach a near-perfect level. Experts pointed out that refined management and continuous technological innovation are the two magic weapons to ensure product quality consistency and stability. From raw material screening to final assembly testing, every step needs to be carried out in strict accordance with international standards.
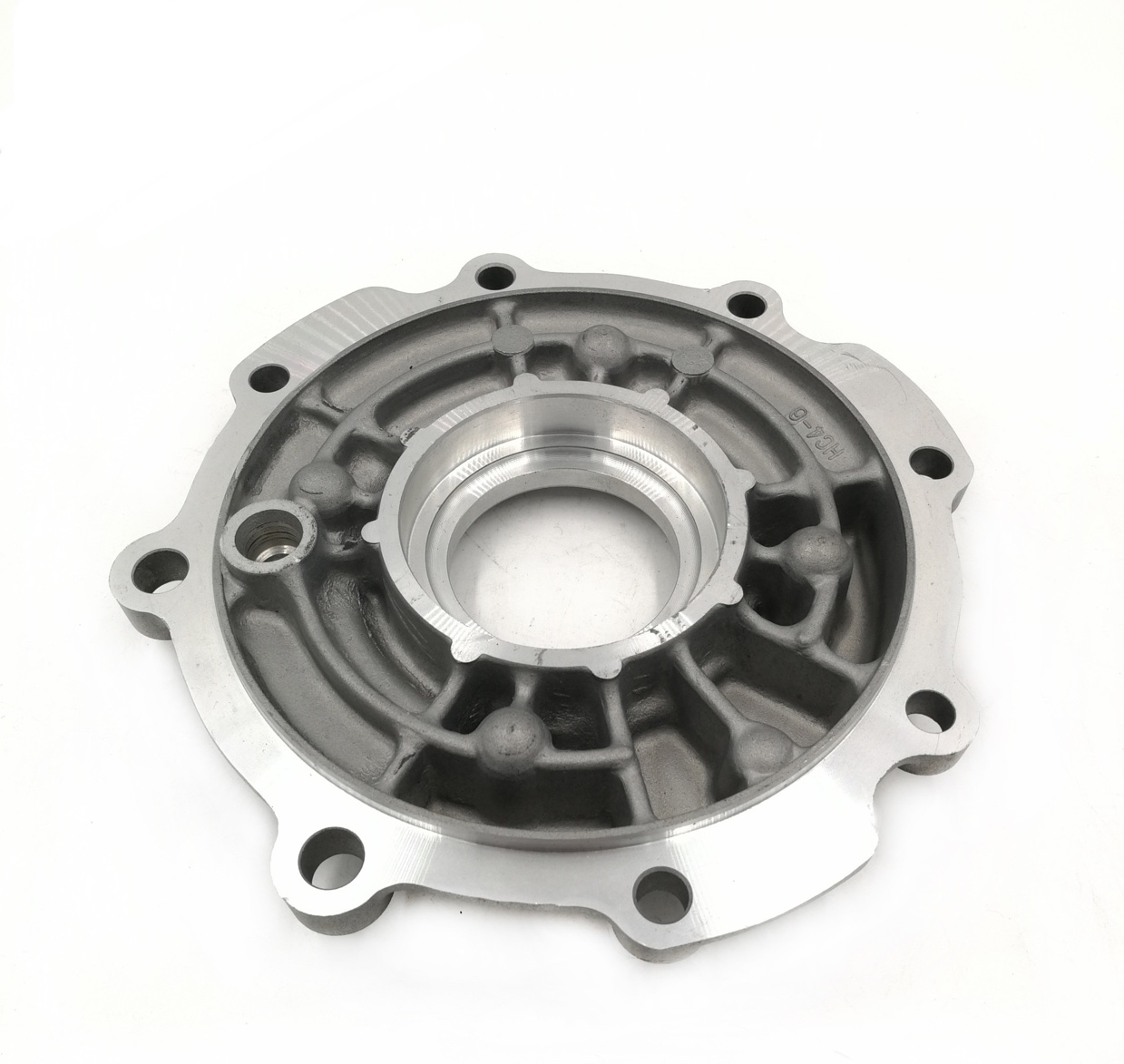
It is worth mentioning that while pursuing excellence, enterprises have not forgotten their social responsibilities. In recent years, significant achievements have been made in the research and development of environmentally friendly new materials. For example, the application of new alloy formulations can not only increase strength but also reduce weight; another substance called "green release agent" has also been widely introduced into the production process. Greatly reduce the impact of harmful emissions on the environment. All these efforts prove that the industry is moving towards a more sustainable development path.
Future Trend Outlook: Aluminum Die Casting Leading the New Trend of Industry Development
With the advancement of science and technology and the development of society, the aluminum die casting industry is ushering in an unprecedented opportunity for change. On the one hand, the changing market demand urges enterprises to keep up with the pace of the times; on the other hand, emerging technologies and ideas also inject new vitality into the industry. At present, the most popular topic is the lightweight body design and the rise of the electric vehicle market. The interweaving of these two forces will have a profound impact on the aluminum die casting manufacturing industry in the next few years and even decades.
In the face of such a changing competitive landscape, research institutions have begun to attach importance to the development of related fields. For example, the power battery shell required for new energy vehicles, the hardware carrier of the intelligent network-connected vehicle system, and so on, are all worthy of further exploration. At the same time, many scholars have called for the establishment of interdisciplinary cooperation mechanism to accelerate the process of achievement transformation. In short, as long as all parties work together to move forward, I believe that the near future will witness a new look of China and even the world's aluminum die-casting industry brilliant chapter!
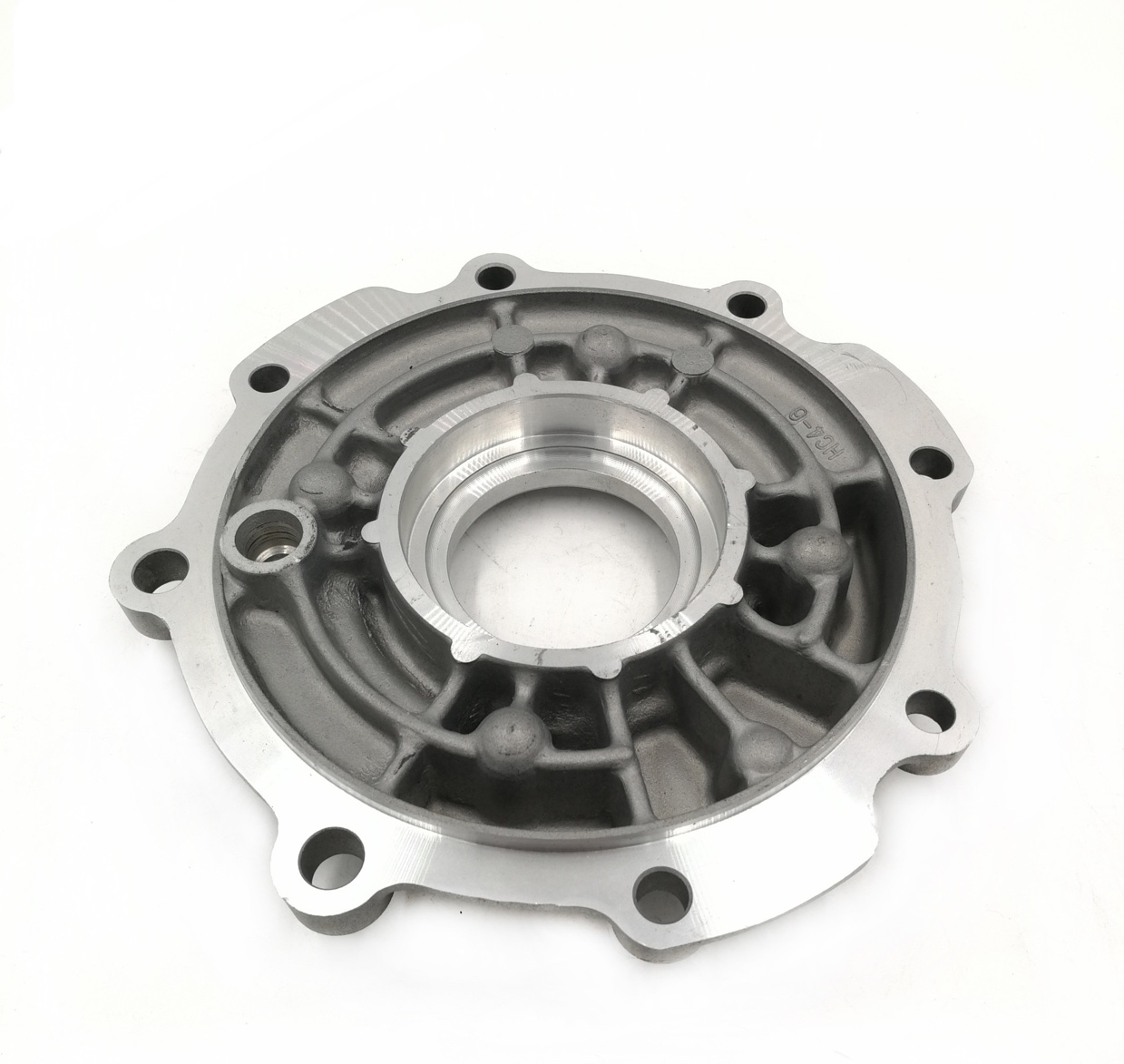